Water Fountain and Sculpture Pipe Repair
Facilites
Quick Links
Our Brochures
For More Information
You can also send us an email and we’ll get in touch shortly, or You Can Call Us: 855-937-6945
Water Fountain and Sculpture Pipe Repair.
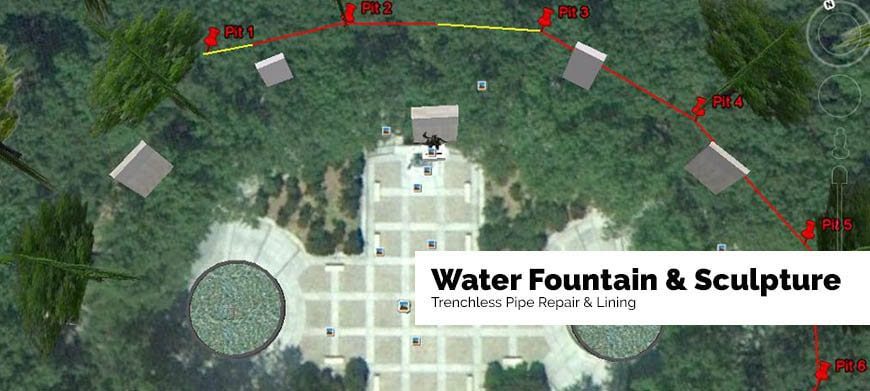
Class A VA Contractor License #2705147099
DMBE VA SWAM # 684641
What is sculpture fountain piping?
We can repair water fountain and sculpture piping without costly excavation. Water sculpture fountain pipelines run vertically and horizontally within and under the water sculpture that they service. Fountain pipelines operate under pressure or suction. It is not uncommon to observe several bends or turns as the piping travels through a fountain or pool. Typical fountain piping can range from 2”- 15” in diameter and is usually made from Cast Iron, Ductile Iron, or PVC.
What happens over time to sculpture fountain piping?
As fountain piping ages the material surface becomes thinner and rougher overtime. Metallic based piping such as ductile iron, which is the most common fountain pipe material, can be vulnerable to surface corrosion from years of chemical and detergent use. As chemical corrosion matures the pipe surface thins and begins to form linear and longitudinal cracks. During the corrosion process the pipe walls become increasingly rough. Surface roughness causes the walls to constrict the fountains piping’s flow capacity. Fountain pipe problems can cause: structural damage of the sculpture, excessive surface staining from corrosion, rust, mold and mildew, excessive leaks, flooding, and sink holes.
At Dynamic Drain Technologies, we use a design first philosophy. Due to the sensitive nature of fountain piping it is vital that we understand and observe all construction, operational maintenance, and structural related details of a fountains piping system. The design process starts with a site survey in which all mechanical components and effluent features are accounted for. Our team of specialists then tag and title any access points needed. These access points provide entry to the fountains piping system. Access is vital and must be considered when moving forward into the video inspection and pipe cleaning phases.
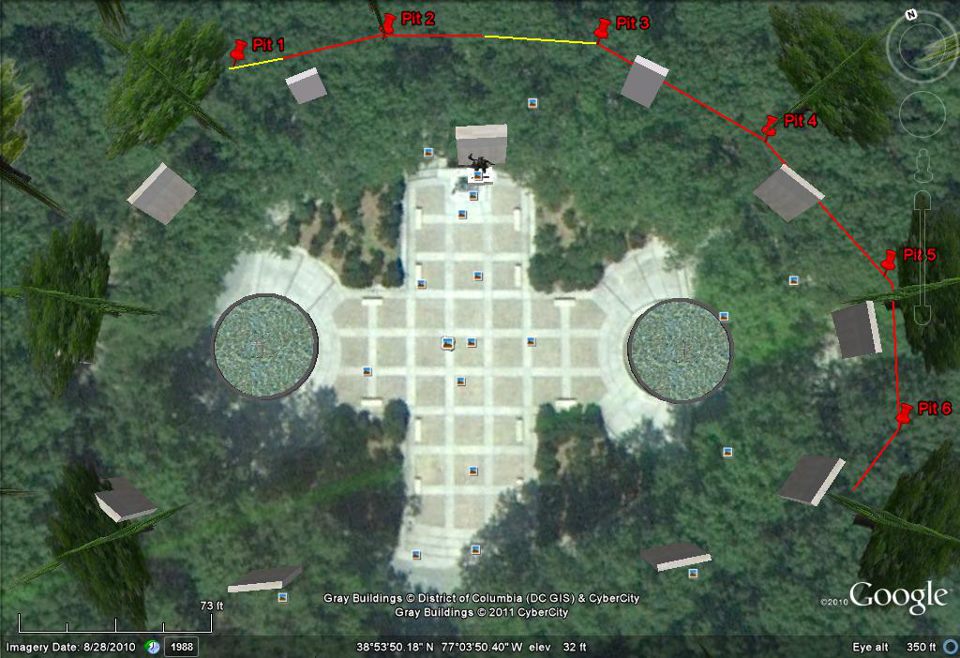
Pipe inspection and location.
Pipe inspections allow us to do several very important things. First and foremost, they allow us to locate and map the piping system. We trace the piping system via a sonde transmitter located in our camera heads. Digital site plans are generated during this process. Pipe inspections also allow us to observe and collect conditional data points of the fountains piping system. This data consists of structural, operational, and maintenance related observations that determine current structural deterioration level of the fountain’s pipe system.
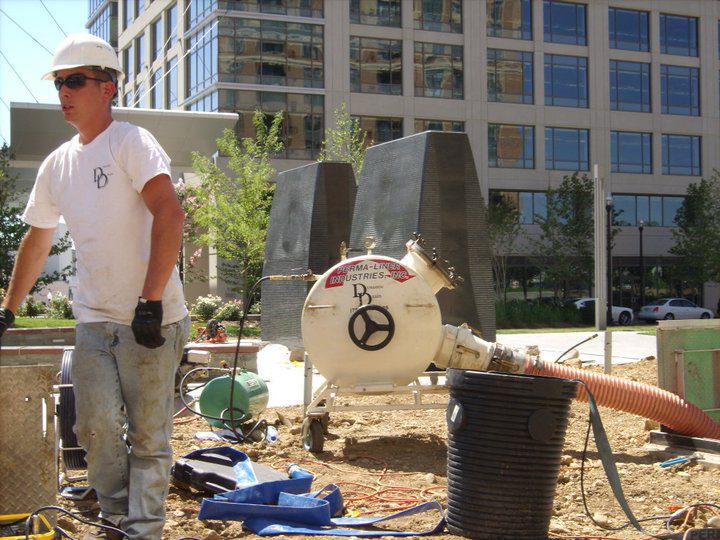
Design
It is highly critical that the survey and design team collect accurate levels of internal pressure and chemical concentrations within fountain pipe system. This information, in conjunction with the fountain pipelines current deterioration level, will allow our engineering team to determine a pressure class and proper CIPP design equation. A design equation will determine how thick our liner needs to be and what epoxies will be used to guarantee long term chemical and physical resistance.
At this point we have all the information needed to present the data and layout the action or pipe lining design. Design will cover the following areas: scope of works, approximate pricing, working hours, project durations, fountain downtimes, pipe cleaning, CIPP liner design calculations, and finally project management requirements and responsibilities.
Pipe Cleaning
The pipe cleaning process requires a remarkable amount of labor and technical expertise. A typical fountain pipe cleaning scenario may call for heavy amounts of mechanical chain knocking or scouring of the internal pipe surface. This process removes years of rust deposits from the pipe walls and surfaces. The dislodged debris are then washed out with forced air or high pressure water jetting. In some cases, debris must be removed through vacuum suction. The desired result of this process is to achieve a clean pipe surface, free of any deposits or roughness that could interfere or interrupt the bonding of the cured in place pipe liner.
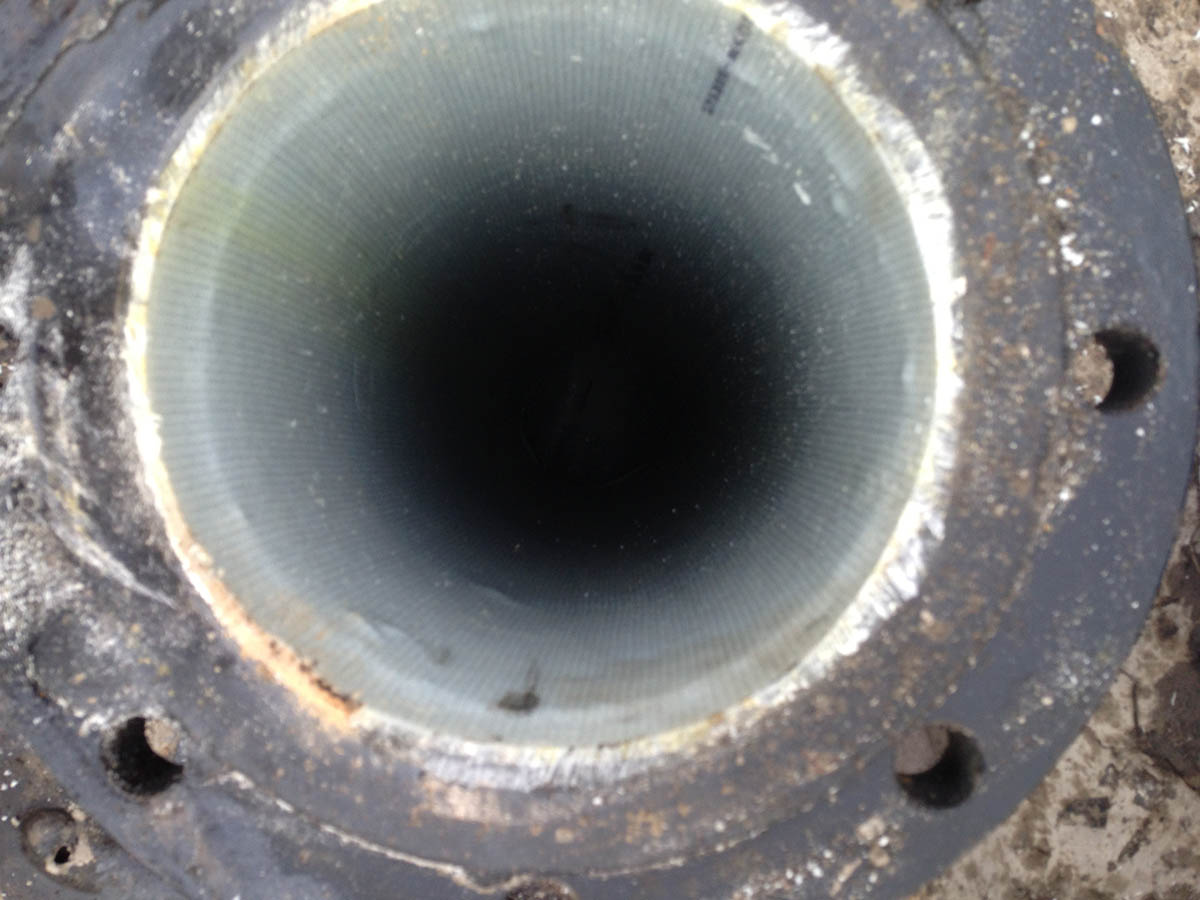
Once the pipe is completely cleaned, technicians then perform another video pipe inspection to record the pipeline before the pipe liner is installed. This is done to show that the pipe was properly prepped and cleaned prior to installing the liner. All lining materials are fabricated onsite using our turnkey job-ready mobile trailer units. Our mobile lining trailers are outfitted with state-of-the-art electric vacuum assisted wet out tables. The liner material is loaded onto the roller table and the epoxy resin is introduced to the liner and passed through the electric roller until the liner has reached 100 percent saturation. In addition to using 100% solids epoxy resin we also will install hydrophilic rubber ends seal for extra long term protection for higher pressure applications.
Now the liner is ready to be loaded into one of our inversion devices and inverted into the pipeline using compressed air. This process is called inversion. For single access installations, a bladder or calibration tube is inserted after the liner and inflated to press the liner against the pipe walls. Once inversion is complete a curing method is implemented. Depending on the application the liner can be cured using 2 methods. The most time-consuming method is an ambient cure. During an ambient cure epoxy resins are combined with an accelerator that will encourage a natural air cure within 3-4 hours of installation. Faster cure times can be achieved by using external heat sources. The quickest external heat source is steam. Forced steam is passed through the liner until the epoxy reaches its desired exothermic flash point. Depending on the diameter and length, using steam can reduce cure times to 1-2 hours.
At the finale of our process we have achieved an internal pipe repair without the need of and demolition. This pipe liner will have 50-year design life and will improve flow capacity. Fountain pipe lining is one of the most cost effective pipe repair options a fountain owner will encounter.